Floor Sealing and Waterproofing
Taking care of your floors is important for their beauty and lifespan. We offer expert floor sealing and waterproofing services that protect your investment from water damage, stains, and wear. Our professional sealing treatments create a barrier that keeps moisture out while preserving the natural look of your flooring.
We use eco-friendly products that are safe for your family and pets while providing maximum protection. Whether you have hardwood, tile, vinyl, or laminate flooring, our experienced team knows exactly what each surface needs. Our floor sealing services help prevent warping, mold growth, and discoloration that can happen when moisture seeps in.
For over two decades, we've been helping Phoenix homeowners maintain beautiful floors that last. Our waterproofing solutions are especially valuable in bathrooms, kitchens, and other areas where water exposure is common. We take pride in delivering quality work that keeps your floors looking great for years to come.
Floor Sealing Process
Our professional approach combines thorough preparation with quality materials and expert application techniques.
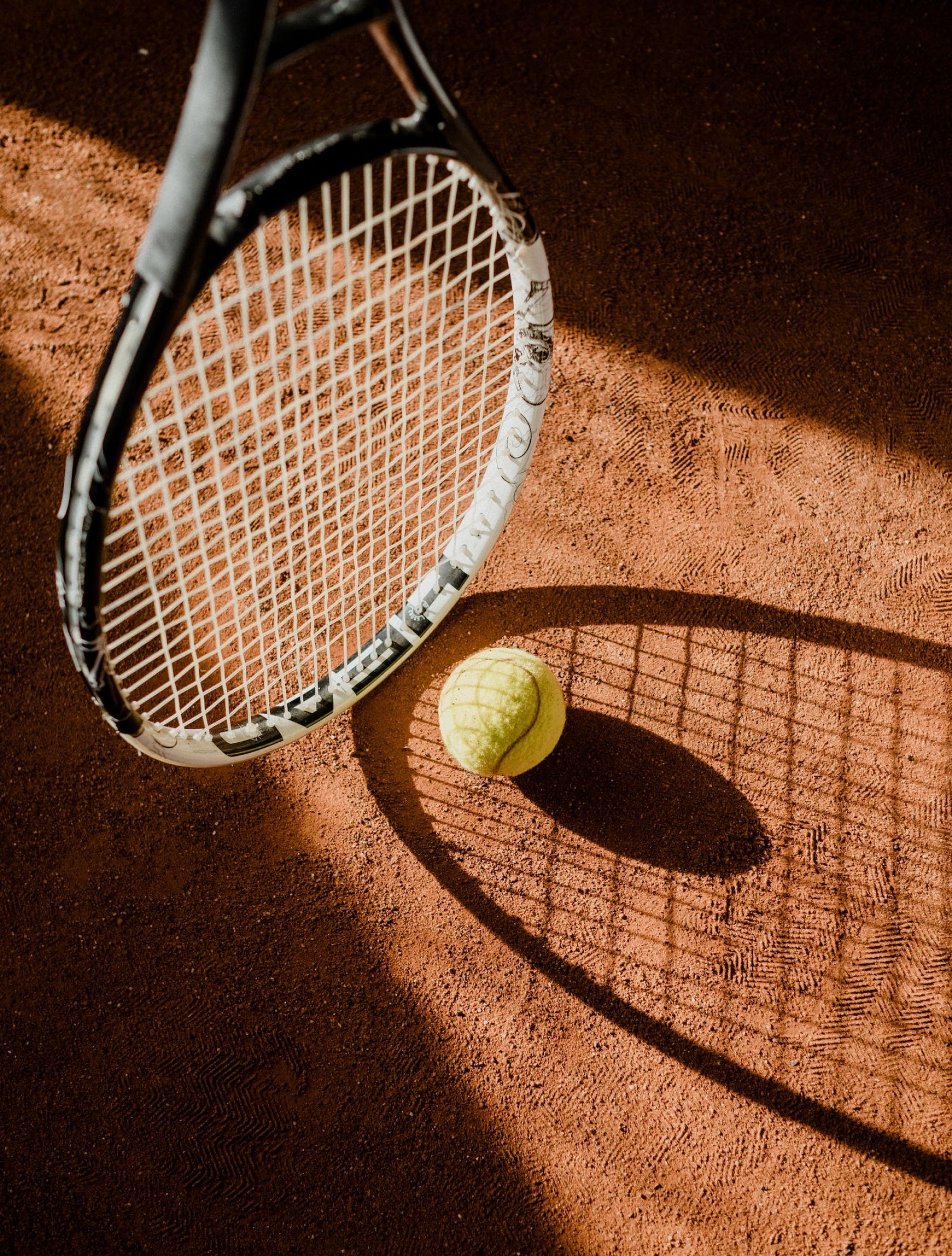
1. Surface Preparation
We begin every floor sealing project with comprehensive surface preparation. This critical first step determines the quality and longevity of the final result. Our team carefully inspects the floor for damages, stains, and imperfections that might affect the sealant's adhesion.
2. Priming the Floor Surface
After preparation, we apply a high-quality primer specifically matched to your floor type and the chosen sealant. The primer serves several important functions:
3. Application of Sealant
We carefully select the appropriate sealant based on:
4. Curing and Drying
The curing process is crucial for developing the sealant's protective properties. We carefully monitor environmental conditions like temperature and humidity to ensure optimal curing conditions.
Waterproofing Techniques
Each technique offers specific benefits depending on your flooring type and moisture exposure level.
Membrane Installation
Membrane waterproofing creates a physical barrier between water and your flooring structure. We use high-quality sheet membranes made from materials like bitumen, PVC, or EPDM rubber. These membranes are carefully applied to the substrate before installing your final flooring.
The process begins with thorough surface preparation to ensure proper adhesion. We then measure and cut the membrane to fit your space precisely. Our technicians seal all joints and edges with special adhesives or heat-welding techniques for complete waterproofing.

Membrane systems are especially effective for bathrooms, basements, and other areas with high moisture exposure. They provide excellent long-term protection and can withstand building movement without cracking or breaking.
Liquid Waterproofing Method
Liquid waterproofing offers seamless protection that conforms perfectly to any surface shape. We apply these specialized coatings as liquids that cure into a flexible, waterproof membrane.
Our process starts with cleaning and priming the substrate. We then apply multiple coats of the liquid waterproofing compound using rollers, brushes, or spray equipment. The material penetrates tiny cracks and creates a continuous barrier against moisture.

This method works exceptionally well for irregular surfaces or areas with many penetrations. The flexibility of liquid systems allows them to handle structural movement without compromising their waterproof integrity.
We use polymer-modified formulations that provide excellent adhesion and durability even in challenging conditions.
Cementitious Waterproofing
Cementitious waterproofing combines Portland cement with proprietary waterproofing compounds to create a rigid, waterproof barrier. This method is ideal for concrete floors and masonry surfaces where structural strength is important.
We carefully mix the waterproofing compound and apply it to dampened surfaces. The material bonds chemically with the substrate, creating a waterproof layer that becomes part of the structure itself. Multiple coats ensure complete protection.
This type of waterproofing is extremely durable and resistant to both positive and negative water pressure. It's particularly effective for basement floors, concrete slabs, and other areas where hydrostatic pressure is a concern.

Our cementitious waterproofing systems include crystalline technology that actively blocks water by filling microscopic pores in concrete with insoluble crystals.
Common Challenges in Floor Sealing and Waterproofing
Floor sealing and waterproofing projects face several key obstacles that can impact durability and performance. Understanding these challenges helps in planning proper installation and maintenance.
Moisture Issues
Excessive moisture is one of the biggest enemies of floor sealing projects. When moisture gets trapped beneath sealed surfaces, it can cause bubbling, peeling, and complete seal failure. In Phoenix, the combination of dry heat and seasonal monsoons creates unique moisture challenges for flooring systems.

We often find that concrete slabs in commercial buildings emit vapor that gets trapped under impermeable seals. This hydrostatic pressure builds up over time and compromises the integrity of the seal.
Efflorescence—those white, powdery deposits—appears when moisture carries dissolved salts to the surface. This not only looks bad but indicates deeper moisture problems that can affect resinous flooring.
Testing moisture levels before installation is critical. We use calcium chloride tests and relative humidity meters to ensure substrate conditions are suitable for sealing.
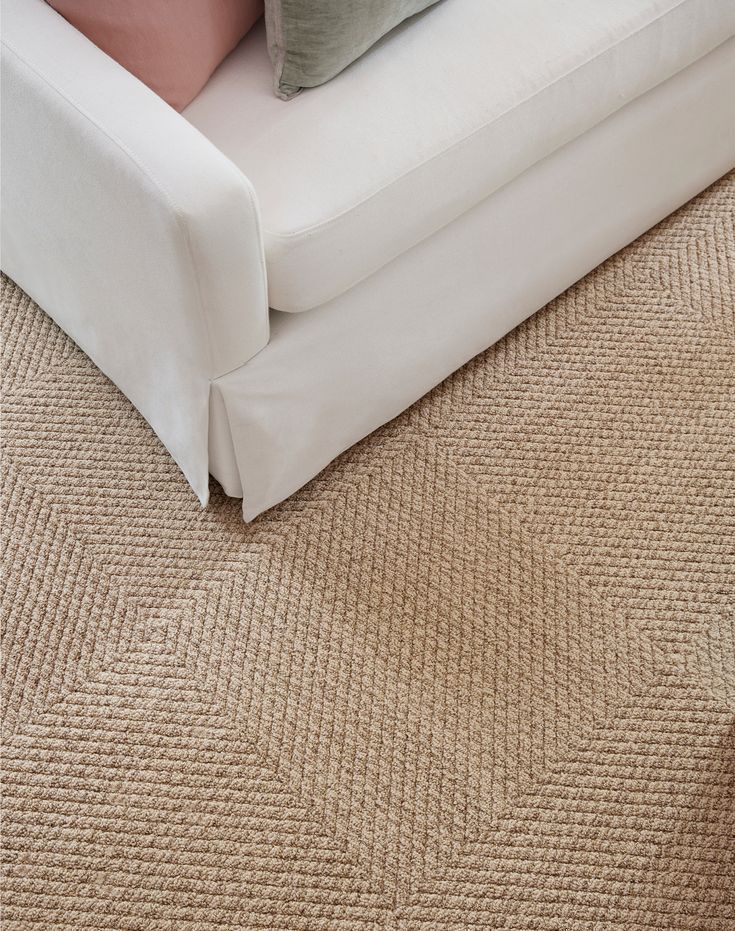
Adhesion Failures
Poor adhesion causes many floor sealing projects to fail prematurely. Sealants simply won't bond properly to surfaces that are dirty, oily, or incompatible with the coating material.

Material incompatibility is especially troublesome. Not all sealants work with all flooring types. We carefully match our products to your specific flooring material to avoid these issues.
Industry experience shows that nearly 60% of floor sealing failures stem from improper surface preparation. We thoroughly clean and prepare all surfaces before applying sealants.
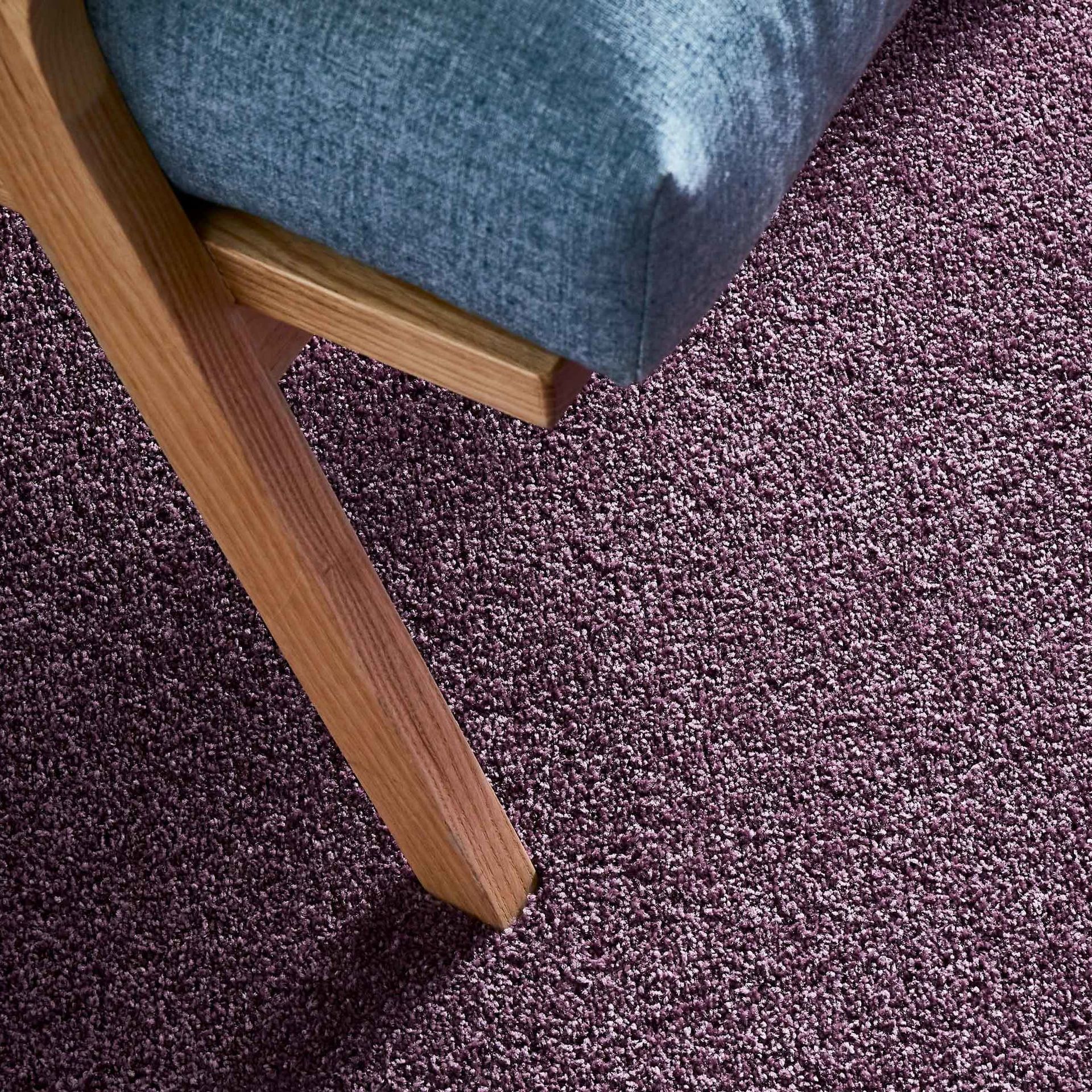
Surface Irregularities
Uneven floors present significant challenges for proper sealing and waterproofing. Cracks, holes, and divots create weak points where water can penetrate and undermine the entire sealing system.

Structural damage must be addressed before sealing begins. Even small cracks can expand over time, allowing moisture to infiltrate beneath the sealed surface. We carefully inspect and repair all surface defects before application.
Temperature fluctuations cause expansion and contraction that stress sealant bonds. Phoenix's dramatic temperature shifts between day and night put additional strain on floor sealing systems.
Self-leveling compounds help create a smooth surface before sealing, but must be fully cured. Rushing this process leads to premature failures. We allow proper curing time between each step of the sealing process to ensure lasting results.

FAQs on Carpeting
Phoenix Flooring Company aims to provide top-quality carpeting and meet customer needs. We offer trendy options and custom solutions to suit different preferences.
How often should floors be resealed?
High-traffic residential areas: every 1-2 years. Bathrooms: every 1-3 years depending on moisture. Commercial spaces: every 6-12 months. Natural stone in low-traffic areas: every 3-5 years. Water drop test indicates when resealing is necessary.
What's the difference between floor sealing and waterproofing?
Sealing provides surface protection against stains and minor water exposure. Waterproofing creates a complete moisture barrier preventing water penetration. Sealing is for stain resistance; waterproofing prevents structural damage. Bathrooms, basements, and outdoor spaces require full waterproofing with membranes or specialized coatings.
What are the signs that my floor needs sealing or waterproofing?
Water absorption (darkening when wet) indicates inadequate sealing. Dampness, white mineral deposits, or musty odors suggest waterproofing failures. Mold along floor edges shows moisture penetration. Warping or discoloration in wood floors indicates water damage. Cracking concrete floors often require repair and waterproofing.